With the industry-wide trend towards horizontal and vertical integration, intelligence is moving from the supervisory control systems to the local components. This development is leading to a growing need for communication for which the open OPC UA standard provides an ideal solution because it can also be used for embedded devices. Softing’s embedded OPC UA server gateway echocollect UA links the control world with the IT world and provides access to process, manufacturing and quality data in more than 50 different controller types. At Kromberg & Schubert – a German automotive supplier – echocollect UA is used for the implementation of product control in a network of plants around the world.
Seamless Data Exchange via OPC UA
Implementation of Product Control in a Worldwide Network of Plants
Kromberg & Schubert supplies a wide range of complex wiring systems, mechatronic and plastic parts for the automotive industry. As one of the leading global providers in this sector, the company is active in more than 30 locations around the world. This global presence poses special challenges with regard to controlling and continuously optimizing the production. The systems used at the various locations need to be networked to enable full synchronization of the machines and equipment with the resource planning and manufacturing control systems. A key requirement is the seamless exchange of data between the control, management and data integration levels in order to forward and concentrate the production data and transfer recipes to the controllers. The fact, that the platforms involved are heterogeneous poses a particular challenge. Kromberg & Schubert uses controllers from Siemens and Beckhoff together with ERP and MES systems. For the implementation of vertical data exchange, Kromberg & Schubert needed a standardized interface for all machines – without having to add further PCs, e.g. as a platform for using OPC servers. The aim was to find a standardized solution that is maintenance free and suitable for long-term use.
Easy Way to Data Integration
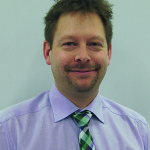
Thorsten Schwartz
Thorsten Schwartz who is responsible for the standardization of process planning at Kromberg & Schubert examined various possible solutions: “We focused our search on the key component; that is the interface between the control level and the management and data integration levels. Important search criteria were the possibility to integrate all the controllers we’re using, the support of a standardized interface for the integration of higher-level management systems, and quick and easy configuration and commissioning.”
His search quickly led him to the echocollect UA server gateway from Softing Industrial Automation which links the control world with the IT world and provides access to process, manufacturing and quality data in more than 50 different controller types. Connection to the higher-level systems is implemented by making consistent use of the OPC-UA standard. echocollect UA features an embedded OPC-UA server that allows to read, write and cyclically access all the data in the controllers. Secure data exchange is ensured by exchanging certificates. As OPC-UA is the further development of an existing and proven standard, the technology employed in echocollect UA ensures a future-proof design.
echocollect UA is designed for easy configuration of the control data. Simple-to-use import and online browsing functionality is provided for leading controller systems, and the user interface is preset with fieldproven default settings. Integrating the controllers requires no adjustments to the control program and thus supports quick and easy commissioning. Changes to the configuration can be made without restarting the installation. In addition to the OPC-UA interface, echocollect UA provides many other features. For example, data can be buffered locally on a memory card to prevent data loss if the connection is interrupted. The data can also be stored in a database and displayed in a visualization interface on any Internet browser. Thanks to the embedded OPC-UA server, echocollect UA has the advantage that legacy machines and equipment with controllers that do not support OPC-UA servers can be integrated into management systems that have an OPC-UA client. This allows the implementation of heterogeneous architectures and solutions without Windows PCs. Once configured, echocollect UA will work for years – untouched, without updates, and with zero maintenance costs. When a device fails, it can simply be reconfigured using the memory card. A system change thus requires only minimum maintenance work by the IT staff.
The easy integration of all the control platforms we use, together with support for data integration and recipe management through Softing’s OPC UA server gateway provides Kromberg & Schubert with a maintenance-free solution, which is suitable for long-term use.
Ideal Connecting Link
Thorsten Schwartz summarizes the reasons behind the decision to use echocollect UA: “For us the deciding factor was the easy integration of all the control platforms we use, together with support for data integration and recipe management. And here echocollect UA leaves no wishes unfulfilled. At the same time, the OPC-UA standard fulfills the requirement for a future-proof solution. This functionality was only offered by Softing’s product.” Kromberg & Schubert is today successfully using echocollect UA to connect the machinery and equipment to the resource planning and manufacturing control systems.
Current Trends in the Industry
The Kromberg & Schubert use case reflects the industry’s current trend where horizontal and vertical integration creates new value chains and business models. The nodes used for data exchange are sensors and actuators that provide interfaces to the real world. This makes it possible to remotely use and process the available data and information. As a result, global and complex networks are being established, which also serve for remote maintenance and diagnostics. They allow the monitoring of installations through the life cycle, including the planning and performance of preventive maintenance action. This offers the possibility to use planned downtimes for updates and device replacement, thus preventing costly production loss. As networks span multiple locations and provide global access, security mechanisms are gaining importance to ensure that only authorized persons can access the installation and influence the production process.
To translate this development into practice, open standards such as OPC-UA- are necessary, which allow a secure high-performance data exchange between multi-vendor automation components. The solutions make use of architectures that are based on services and provided centrally over the Internet. In the long run these developments are expected to lead to the implementation of the “Internet of Things” for factory environments, as envisaged in the “Industrie 4.0” concept. There all machines, warehouse systems and operating resources will be globally networked and will be available to products with decentralized intelligence; these products will be manufactured autonomously as part of local optimization, they will be uniquely identifiable and their state and location can thus be determined at any time.